Whether it’s a cheapo plastic recreational kayak, a tough-as-nails whitewater playboat, or a long, sleek touring rig, there are a wide variety of kayak materials and construction techniques out there.
The science behind these construction techniques and materials could fill an engineering textbook, so I’ll try and break things down in simple terms.
If you’re interested in what kayaks are made of, this post will delve into various kayak materials, their strengths, and weaknesses, how they’re manufactured, and hopefully, help you select the right kayak material for your needs.
What’s the Best Material For a Kayak?
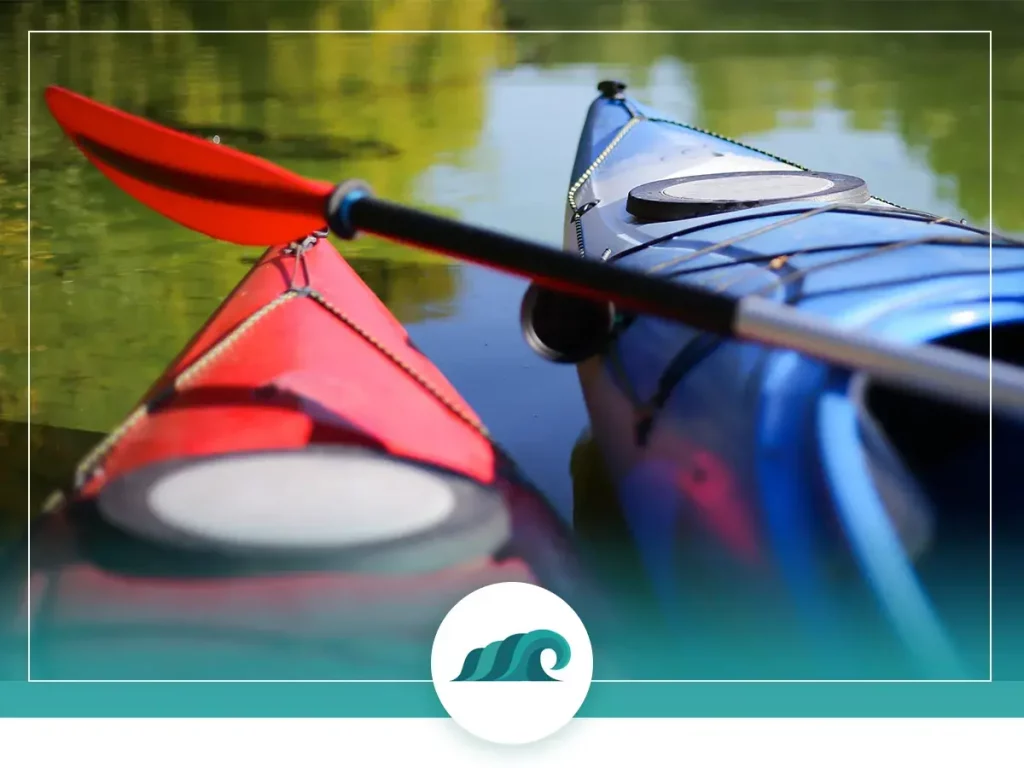
The best kayak material will largely depend on use case, budget, weight, and durability requirements. Just as with other sports equipment like mountain bikes or skis, it’s important to consider the tradeoffs between durability, weight, and cost.
Before selecting a kayak material, some good questions to ask yourself are:
- Where do I plan to use the kayak? Inshore? In the ocean? Perhaps, whitewater rivers?
- What’s my skill level and commitment to the sport? Do I want a kayak for occasional recreational use, or will I be taking it out for challenging sea expeditions?
- How much space do I have for storing the kayak? What are the kayak’s dimensions?
- How do you plan to transport the kayak? Roof rack? Will it be light enough to carry to the water or mount on a roof rack?
- How much am I willing to spend?
To help you answer these questions (and more), I’ll break down the typical kayak materials, and how they play into these key decision factors.
Kayak Materials
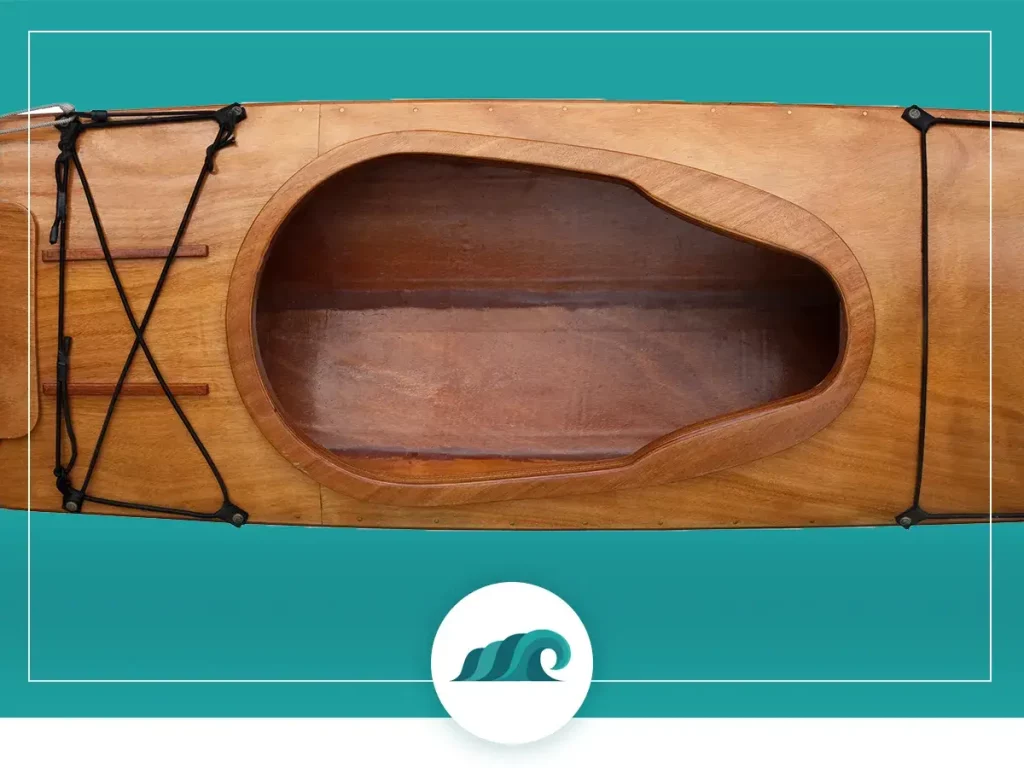
Kayaks have been around for a long time – a really long time. In fact, the first kayaks were built by the Arctic Inuit people dating back at least 2000 years. They were primarily used for fishing, hunting, and transportation.
These early kayaks were made from sealskins stretched over driftwood frames. The seams were waterproofed using boiled seal or caribou fat. Despite these primitive materials, these early kayaks were highly capable and seaworthy.
Modern kayaks borrowed heavily from these Inuit designs and improved on them using modern materials and construction techniques.
Wood
Wooden kayaks most closely resemble their early rib and cross frame progenitors. They’re made of durable marine grade wooden frames with wooden decks and hulls. To prevent warping and water damage, their typically coated in fiberglass, resin or varnish to protect the wood underneath.
Wood is fairly durable, lightweight and aesthetically beautiful. Despite many people’s assumptions, it’s actually as strong as – or stronger – than composite materials. Although it’s fairly durable, it’s not the ideal material if you plan on kayaking in rocky rapids or whitewater environments.
Although they’re highly capable watercraft, wooden kayaks aren’t that commonplace. Many kayak buyers don’t even consider wood when selecting a kayak material. The main reason being wooden kayaks typically require some woodworking skills to assemble (or paying an expert to custom build one – which can cost some serious dough).
Fortunately, there are now many “stitch-and-glue” models available. These are fairly easy to assemble yourself and require minimal woodworking skills. If you’re more of a do-it-yourself type, you can also purchase schematics for a small fee – and then build the kayak from scratch.
Wood Kayak Pros:
- Aesthetically pleasing – these kayaks are absolutely stunning.
- Lightweight, as durable or more durable than composite.
- Fairly easy to repair.
- Great project for DIY enthusiasts and woodworkers.
Wood Kayak Cons:
- Not ideal for rough whitewater conditions.
- Requires assembly and woodworking skills.
Rotomolded Polyethylene
Most of the recreational kayaks available today are made from rotomolded polyethylene. Polyethylene is an incredibly durable, flexible and impact resistant material, and is able to withstand seriously hard knocks.
The term ‘rotomolded’ refers to the manufacturing process – in which plastic pellets are heated, poured into a two-part mold and then “tumbled” in an oven. This process is fairly straightforward – especially compared to the layering required for other methods – which makes polyethylene the least expensive kayak material.
The resulting material will flex and bend rather than break. This makes polyethylene kayaks the ideal choice for whitewater and rapids. However, unlike other materials, poly is fairly difficult to repair once a serious puncture is formed.
Another downside is weight. Polyethylene tends to be the heaviest kayak material, which makes it a poor choice for kayakers looking for serious speed or long distance touring. The material is also susceptible to UV damage, which makes coating with a UV protective layer a must.
Polyethylene Kayak Pros:
- Flexible, durable, and impact resistant. Tends to bend rather than break.
- Relatively inexpensive.
- Ideal choice for rocky, whitewater conditions.
Polyethylene Kayak Cons:
- Polyethylene is generally the heaviest kayak material.
- Difficult to repair.
- Susceptible to UV damage. Can warp or deform from too much sun/heat.
Composite
Composite – commonly referred to as fiberglass – is actually constructed from several layers of graphite, Kevlar, and carbon fiber, or some combination of the three.
The manufacturing process involves layering various fabrics on top of one another and then applying to a mold. The various layers are then vacuum sealed and allowed to cure, before forming either the deck or the hull. Finally, the deck and hull are fused together to form the final product.
Due to the wide variety of material options and configurations available, many variations in strength, weight, and overall performance are possible. Generally, graphite blends will be the lightest – and the most expensive.
Overall, composite kayaks are extremely lightweight, fairly durable, and offer the best performance in the water. Tracking, responsiveness, and efficiency will be markedly improved over typical plastic recreational kayaks. This type of performance comes at a cost though – composite is the most expensive kayak material on the market.
While composite hulls are fairly durable, they’re not meant to handle serious direct impacts from rocks and the like. If they do sustain damage, they’re actually fairly easy to repair in the field using fiberglass fabric and resin.
Composite Kayak Pros:
- Ultra-light. Great for long-distance voyages.
- High-level responsiveness, tracking, and speed.
- Fairly durable – similar to wood.
- Many configurations are possible with blends of graphite, Kevlar and carbon fiber.
- Fairly easy to repair.
Composite Kayak Cons:
- Most expensive kayak material.
- Stiff material is susceptible to damage from direct impacts.
Thermoform
Thermoforming is a newer manufacturing process, which involves creating a multi-layered sheet of plastic, which is then drawn over a mold and formed into either the hull or deck (which are later fused together). This technique fuses several plastic layers together – typically a base layer of impact-resistant ABS plastic with one or more weather resistant acrylic outer layers.
The resulting material offers excellent durability, is nearly as lightweight as composite, and only costs slightly more than polyethylene. Thermoform is rapidly becoming the go-to choice for intermediate-level kayaks.
The acrylic outer layer provides excellent UV resistance, making these kayaks able to withstand hot, sunny conditions. It also gives the boat a bright, lustrous shine – making them an attractive choice.
Thermoform Kayak Pros:
- Lightweight, durable, and impact-resistant.
- Provides a similar level of performance to composite at a lower price point.
- Recyclable.
- Outer layer provides UV protection – plus it’s highly aesthetic.
Thermoform Kayak Cons:
- Acrylic outer layer can break down over time.
Inflatables
Inflatable kayaks are typically made from tough and durable drop-stitch fabric. Drop stitch construction makes them able to withstand high inflation pressures and provides a decent level of puncture resistance.
Like rafts and catarafts, inflatables are generally made of either PVC or Hypalon (polyurethane).
PVC is inexpensive, fairly easy to patch, and can be cheaply “welded” together during construction. However, it’s not very resistant to UV damage, abrasion, or extreme temperatures. This means you’ll need to store it away from direct sunlight and make sure it’s coated in a UV protective spray. Check out the Intex Explorer K2 for a solid budget inflatable.
Hypalon is tough, resistant to extreme weather, and can withstand harsh UV radiation. It’s also resistant to environmental factors like mildew and fungus. It’s more expensive than PVC because the seams must be hand glued – which adds a hefty labor cost to the manufacturing process. Hypalon is the material you’ll find used by the U.S. Coast Guard and Navy in dinghies and zodiac boats.
Either way, inflatables provide excellent portability and versatility, making them an excellent choice for backpacking and camping.
Inflatable Kayak Pros:
- Ultra-light and portable. Can fit inside a duffel bag or large backpack.
- Great for backpacking, trekking, and camping.
- Drop stitch construction provides a rigid frame and puncture-resistance.
- Fairly inexpensive.
Inflatable Kayak Cons:
- Susceptible to puncture and UV damage.
- Will not track or perform as well as a hard-bodied kayak.
How are Kayaks Made?
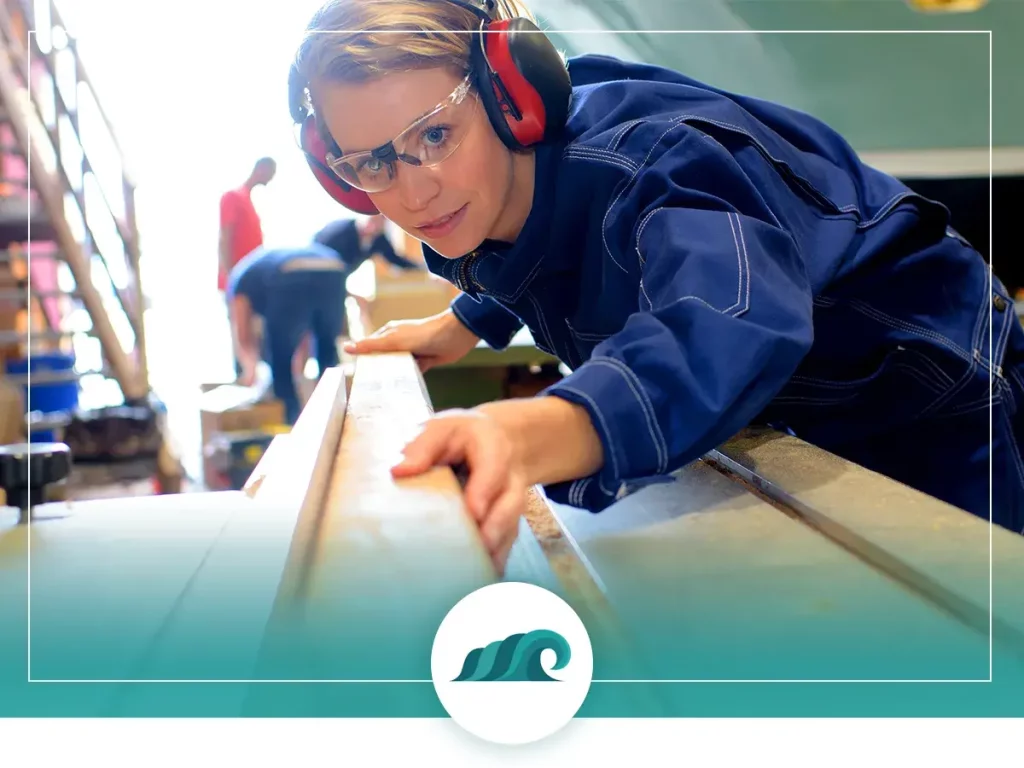
Wood
‘Stich-and glue’ construction is the most commonly built style of wooden kayak for do-it-yourselfers.
The process involves joining pre-cut plywood panels along their edges with epoxy and fiberglass. This type of assembly eliminates the need for complex frame construction and joinery. The process does take some time though, as you need to wait for each panel to dry before attaching the next one.
The plywood panels are first wired together through precut holes, and then a thickened epoxy resin is applied to completely seal the panels together and create a watertight seal. A fiberglass sheet is then added to increase overall strength and abrasion resistance.
The last step is applying several coats of marine grade varnish to seal the wood from water damage. The resulting look is a beautiful, lustrous mahogany exterior that really catches the eye.
Check out this video for an in-depth look into ‘stitch-and-glue’ kayak construction:
Polyethylene
Polyethylene kayaks are constructed through a process known as rotational molding or rotomolding.
This process begins by placing polyethylene resin pellets or powder, as well as coloring agents, inside the bottom half of a two-part aluminum mold. The two parts of the mold are then sealed together and the mold is rotated inside an extremely hot oven – causing the melted polyethylene to evenly coat the inside of the mold.
After a few minutes, the mold is moved to a cooling chamber, where it continues to rotate and cool off. As the kayak cools, it shrinks and pulls away from the mold. After a few minutes, rubbery hot kayak emerges, which is then supported while it hardens and shrinks down to its final size.
Composite
Composite kayaks are manufactured by hand fitting layers of fiberglass, Kevlar, and carbon cloth into a gel-coated mold. Stiffening agents are then added to high impact areas inside the mold, and finally, resins are used to thoroughly saturate all of the materials.
There are several different processes used to bind the materials together.
Often, a vacuum bag is placed around the mold – which is then sucked dry – causing all of the layers to bind together and squeeze a high proportion of resin out of the mold. This results in a desirable cloth to resin ratio and lowers the kayak’s weight.
This binding process can also be performed with hand tools, which leads to a higher cloth to resin ratio, but it still will perform excellently.
Thermoform
Thermoforming is similar to polyethylene manufacturing, but with several added steps.
Rather than being formed inside a rotating mold, the resin pellets are first extruded into a flat sheet. Additional layers of compatible materials are fused together with the base layer to create a tough, lightweight material.
Typically, the outer layer is a modified acrylic, which provides excellent UV resistance. The base layer is usually some form of high impact ABS plastic.
The molding process itself involves heating the layered sheet and forming it over a ‘male’ mold. This is done separately for the hull and deck, which are later fused together to create the final product.
This process is less labor intensive than the process used for composite boats, which makes the final product significantly less expensive.
Check out this quick look at the thermoforming process:
Wrap Up
Hopefully, you now have a better grasp on kayak materials and their manufacturing processes.
Keep in mind there’s no best kayak material for every situation. Every material has its relative strengths and weaknesses, so it’s important to determine how and where you plan to use the kayak before selecting a material.
Another important consideration is the ease of repair. If you’re planning on longer overnight kayak trips, then you’ll want a kayak that’s fairly easy to patch up in the field.
Lastly, cost is an important consideration. There’s no point in splurging on a high priced composite touring kayak if you’re just going to paddle around tranquil fishing ponds.
The next time someone asks you “what are kayaks made of?” you’ll be well equipped to answer them.